The Unique Device Identification (UDI) is demanded by the regulations MDR 2017/745 in article 27 and in the IVDR 2017/746 in article 24. The UDI is an identifier used to increase transparency, traceability, and safety. Read here how to implement the process of UDI creation into your QMS.
What's the UDI for?
The UDI is a required identification, made of an alpha-numeric code which is human- and machine readable.
The UDI is intended and used for:
- identification of the medical device
- identification of the chain of custody of a medical device
- improved transparency
- identifying issues during post-market surveillance and safety-related actions
- combat counterfeit products
- share data on clinical outcome and safety of a medical device
Why to include the UDI into the QMS?
The simplest argument on this is, as it is required by MDR 2017/745 and the IVDR 2017/746 in their article 10.
Whatsoever, the UDI is to be applied to the medical device over it’s entire lifecycle. Thus, the UDI is not only affecting the development of novel products, but is to be incorporated in post-market activities and maintenance of the device.
Further, the Medical Device Coordination Group (MDCG), as an expert group of EU member states representatives, published a guidance on the integration of the UDI within an organization’s QMS. Even though the guidance from the MDCG is not binding, it gives another guidance on how to include the UDI into the QMS of a manufacturer of a medical device.
How to include the UDI into the QMS?
As any QMS, whether ISO 13485 or another, relies on a process approach, the best practice is to implement the UDI process-oriented. Based on the commonly known Plan-Do-Check-Act (PDCA) cycle, the processes for UDI can be implemented accordingly. In principle, follow the steps below for a seamless integration into the existing QMS.
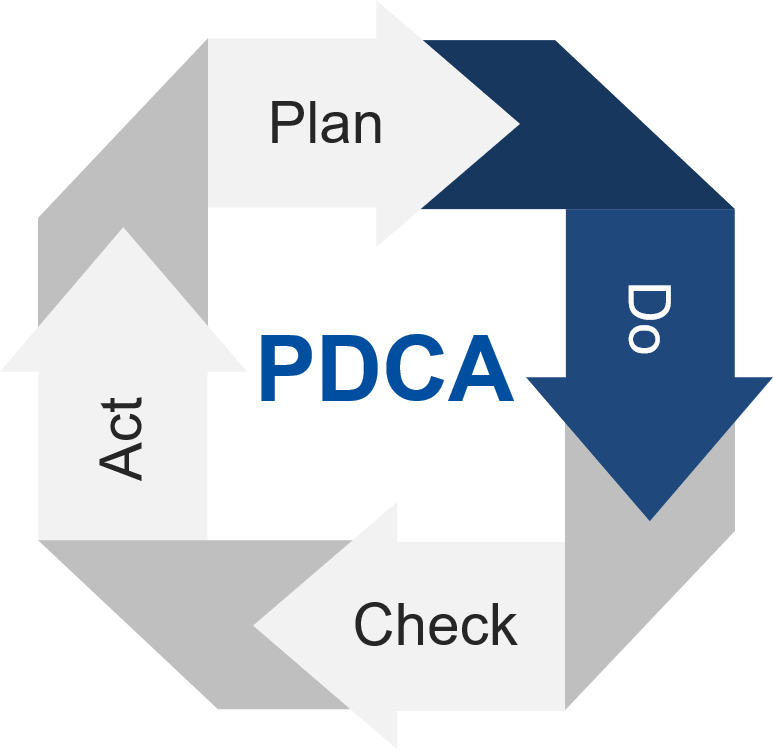
- Plan the implementation of the UDI by analyzing requirements, issuing entities and stakeholder needs
- Do decide on the best fit for an issuing entity and define the internal processes and RACI (Responsible, Accountable, Consulted, Informed)
- Check and the implementation of the processes and monitor the UDI per product over the lifecycle
- Act on the processes and methods implemented to keep compliance high
By when to implement the UDI?
The implementation of the UDI is risk-based. With this, the timing of the implementation is based on the risk classification of the medical devices.
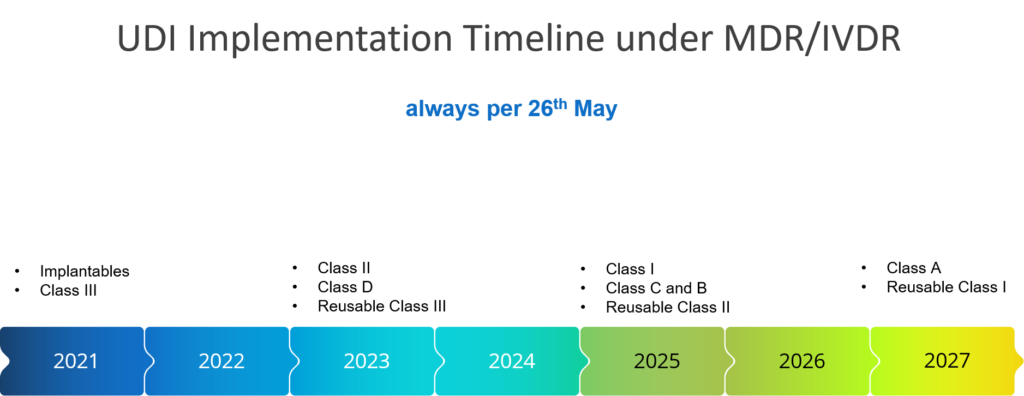
As implantable and Class III medical devices have already passed the deadline of UDI implementation, other’s are still to come. To be mentioned are reusable medical devices, on which an UDI placement on the medical device itself is necessary two years after deadline of the UDI. This UDI on re-usable medical devices is sometimes referred to as direct marking.
Act now and start immediately with the implementation of these requirements as the clock is ticking. In case of needed support or interested in outsourcing the task, contact Avanti Europe.
How Avanti Europe can help
Avanti Europe’s Experts have a decade-long track record and expertise in consulting and hands-on working in process implementation in the Pharmaceutical, Cosmetical, and Medical Device industry. Our experts support your company with hands-on workforce and support in UDI-process implementation, risk-based process design, documentation, and training for the company staff. Visit our online shop for checklists and other services.